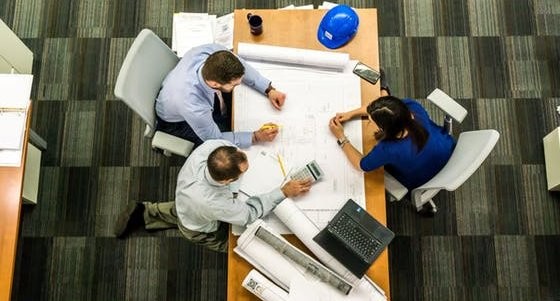
Why is it so hard to get commitment for first-rate FMEA methods in most organizations? Why don't more companies encourage the proper use of a tool that creates a deep, powerful understanding of risk in designs and processes? Why do they frequently—even usually—treat FMEA as an after-the-fact check-the-box exercise?
Here are the top five closely-related reasons why FMEA doesn't get the respect and emphasis it deserves.
1. Problem prevention doesn't get much love from managers or executives.
When you prevent a problem, who recognizes your effort? Managers tend to respond when something unexpected comes up. And the most common unforeseen event in design and manufacturing is something that goes wrong after a new product is out in the marketplace. More to the point, everyone tends to get excited about solving problems. Problem solving is challenging, it's often intuitive, and even exciting. When you solve a problem, you get praise and, in some cases, significant rewards. Preventing problems—which is what FMEA is all about, really—is usually invisible as far as managers are concerned. After all, how many businesses launch new products or services and expect something to go wrong? When nothing happens, that's not news. "It was your job to get this done and not have problems. Why should you expect to be recognized when you did just that?"
2. Quality rarely has a seat at the main table.
At the executive level, how often is quality considered as part of the strategic mix? Quality tends to take a back seat to material cost reduction targets, market share gains, and manufacturing productivity improvement. Even in businesses that claim to be quality-driven, quality is usually an afterthought in terms of strategy. If quality goes bad, then executives want to know what went wrong, and, in too many cases, "what went wrong?" is just code for "who made this mistake?" I don't think it's realistic to push for quality as the most important strategic issue; that simply won't resonate with many executives. But it's not unreasonable to expect quality to be a serious consideration in trade-offs with cost and schedules. If the benefits were easier to see, this imbalance might be less common.
3. Cost savings from quality improvements are often too small to compete with productivity gains and cost reductions.
While it's often true (more often than many people realize) that designs and manufacturing processes that are problem-free can cost less than design-manufacturing packages that are buggy, it's not always true. And executives tend to focus on and remember cost increases that prevent failures. When this happens, the numbers don't favor quality. If you have an issue that affects 3% of your products, that's a big problem. Let's you plan to produce 1,000 units of something, and fixing that 3% of defective product out in the marketplace costs $20 per unit. If you do the arithmetic, any standard cost increase greater than $0.60 per unit will add more to total cost than all of the "field fix" cost recovery. Worse, adding cost before production starts is a certain cost while the $20 per unit losses may or may not happen. It's hard to be sure before customers actually start using the product, and even then, they may not all notice the issue or complain about it.
4. Prevention work like FMEA takes time and energy.
Getting new products developed and launched is a lot more exciting than the relatively deep thought required to truly comprehend risk. And, to be fair, every business is under a great deal of pressure to keep their products fresh and competitive. Taking the time to determine what might go wrong—and then to figure out what could be done to avoid those things—is often seen as a barrier to getting products into customers' hands. Delays can cause major market flops, so the pressure is always on to go faster and to do that with fewer people, less analysis, less testing, and less money. If you gloss over DFMEA or PFMEA and nothing goes wrong, you'll be tempted to do it again. Sooner or later, something you didn't think of will cause big trouble. It's unlikely, though, that anyone will connect weak FMEA work with the problem. In sum, acting is more attractive than methodical thinking, and FMEA is all about analytical thought.
5. Almost no one really believes that they'll make mistakes when planning new products and new manufacturing processes.
I've never met an engineer who openly and candidly admitted that he or she was releasing work that likely had some flaws. In fact, it's rare to meet an engineer who even believes in his or her heart that their work is imperfect. After all, why would anyone design a product or plan a manufacturing process so that it might go wrong? You wouldn't have chosen a given screw class, thread, and size unless you thought it was the right fastener. If it later turns out to be a bad call, well, things happen, right? Confronting the potential that your work is less than perfect is hard on your ego, and it takes a very thoughtful development team to embrace that very real possibility.
In sum, there's an extremely deep and instinctive tendency in most people to avoid looking at the darker side of things. And make no mistake, it isn't easy to face up to the imperfections that are present in most development projects.
But there is a solution that clears away these issues. You can go faster, you can confront risk without mental baggage, and you can find cost-effective solutions that overcome most of these issues. That solution is to use good technique in creating and using deductively-based FMEA studies. Using sound methods addresses all of these reasons that people don't like FMEA very much. And who knows, if you develop a real skill for FMEA methods, you might even find that FMEA can be a fascinating and engaging way to look at things.
You can learn more about good technique in both DFMEA and PFMEA in other Lighthouse posts.