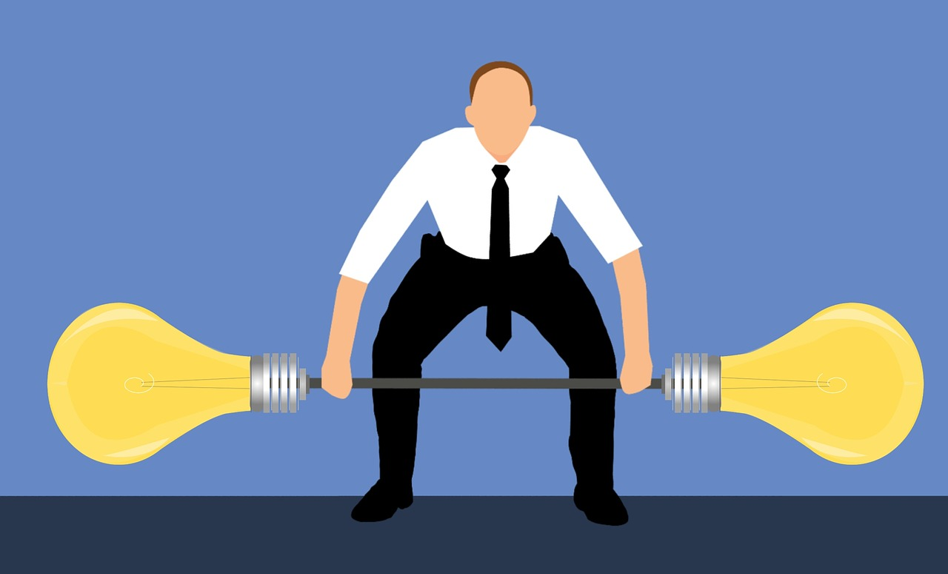
Since I first completed a detailed FMEA study in 1978, I’ve wrestled with a simple question.
And, at the same time, I’ve heard this question from others again and again and again.
The question usually starts with an assertion: “You know that this FMEA business is a great deal of work.” At the same time, the unspoken part of that statement is “And I really don’t think it’s worthwhile.” So, the question really seems very uncomplicated and straightforward.
Is FMEA really worth all of the effort and time you have to put into it?
Forty-one years after my first serious FMEA study, I think I can offer an answer. To begin with, this is a not a simple question. However, to paraphrase American satirist H. L. Mencken, for every complex question there is a simple answer—and it’s wrong.
With that in mind, let’s look at the value of FMEA from several viewpoints.
The first is a question of scope.
If you look at DFMEA or PFMEA in terms of scope, deciding on the depth that’s necessary for a worthwhile result can be daunting. I’ve explored this a bit before in my article from 19 December 2017: Understanding Scope. You can lose all sense of proportion if you choose a scope of excessive depth, or you can render an FMEA almost valueless if you choose a scope that is too limited.
How can you decide what’s appropriate?
I hinted at this in my scope article, but during the 9 plus years I spent working at Lennox on heating, ventilation, and air conditioning equipment—and with the help of outstanding professionals at Lennox—I gained more insight. It started with a concept I first heard from Steve Brown, a world-class reliability expert. He introduced me to the idea of a “NUD”—something that was New, Unique, or Difficult. Later, another exceptional reliability engineer at Lennox, Joe Powell, suggested that we could narrow the scope of any FMEA by simply limiting our range to those elements of process or product that included “NUD’s.”
This idea worked very well, and, while I can’t reveal the details, by applying this concept, we were able to resolve several major issues over time. In addition, it’s also clear that we avoided an even larger number of potential problems that would have been overlooked if not for the use of FMEA. In addition, we kept the effort to complete needed FMEA work to a reasonable level.
The second point I’ll add is closely related to the question of scope and “NUD’s.”
In any FMEA, even one where the focus has been limited to issues that are new, unique, or historically difficult, a good deal of the causes and controls that will be developed when using deductive techniques will be things you already know about, have already dealt with, and/or currently have proven controls to limit risk.
To what degree is this true? In my experience, even with relatively new technology, 60 to 85% of the FMEA output isn’t surprising in any meaningful way. For mature technology, the range is closer to 80 to 95%. As a result, we can say that somewhere in the range of 5 to 20% of the output—the understanding of cause-mode-effect chains and the corresponding control strategies—will deal with something that hasn’t been considered before.
This still isn’t the end of this trail, though. Of the 5-20% that is new, perhaps only 10 to 20% really poses a significant risk, as suggested by either a Risk Priority Number (RPN) pattern or the new “Action Priority” tables that are being adopted by the US and German automakers.
When you add all of this up, you start to realize that there might only be two or three cause-mode-effect chains in a 100-line FMEA study that are revealing something important. And important means something you didn’t know about or really understand very well even if you knew about it as well as something that leads to a meaningful risk.
Does all of this lead you decide if FMEA is worth the effort?
The answer is still unclear, no matter how much you might want a simple answer for this complex question. The reason is that an occurrence of 100% is preposterous in almost any conceivable situation. In fact, occurrence ratings greater than 4 or 5—except in the most cutting-edge situations (say, space flight equipment)—should be rare.
An engineering team that chooses a process step or a design element that will likely have an occurrence of 6 or more really needs to step back and rethink what they are doing. (I have seen a handful of situations where that’s been true, and everyone involved has been very grateful that the issue was exposed before any commercial product was released for sale. )
In 99% of the FMEA’s I’ve observed (and my count is in the thousands) the net risk is uncertain. The severity may be high, but if the occurrence isn’t highly probable, does the amount of resource expended on the FMEA make sense? Given the usual difficulty in accurately assessing occurrence, it’s just not easy to say yes or no.
To me, this is very similar to placer techniques for gold mining. You have to dig tons (or tonnes) of earth to sift for a few ounces or grams of gold. Gold is extremely valuable, though, and so placer mining is widely used.
Nevertheless, this analogy falls apart for a simple reason. Gold has what might be called a “positive” value. Finding and preventing problems, which is what FMEA does, tries to avoid problems and attendant costs—a “negative” cost or cost-avoidance.
This brings us to one of Dr. W. E. Deming’s most profound ideas:
You can’t measure everything. Here are two of his pivotal ideas on this subject:
3% of the problems have figures, 97% of the problems do not (sounds about right to me). The most important figures that one needs for management are unknown or unknowable (Lloyd S. Nelson, director of statistical methods for the Nashua corporation was the originator of this idea).
It is difficult—not impossible, but uncertain at best—to estimate cost-avoidance. And I know this kind of calculation doesn’t usually resonate with financial specialists, although I’ve met more than a few who understand this. However, the connection between the engineering resource commitment and the cost avoidance are so separated in time that executives often lose track of the cause-and-effect relationship that exists between prevention actions and cost avoidance.
Finally, and perhaps most significantly, in any large and multifaceted organization, seeing and understanding all of the implications of prevention activities, like FMEA studies, is rare at the executive level.
It’s hard to see how prevention work led to something that never happened! And so there’s quite often resistance to prevention-oriented expenditures.
I suspect these dynamics are part and parcel of every major product recall and/or major blunder that companies around the world have had in the past and even those that are now unfolding. (You can offer your own examples—there are plenty to cite.)
The net result is therefore unclear. I’m very convinced, based on a long career (in which FMEA has been prominent but by no means dominant) that FMEA studies, particularly when scoped properly, are a very wise use of time and money.
I’ll add one more caveat, though. The studies must be done well using deductive methods, with a rational scope, and within the scope selected, done thoroughly and without manipulation.
If those three criteria are not met, all bets are off—and FMEA is not worthwhile. Done well, though, FMEA is a wise and prudent expenditure.