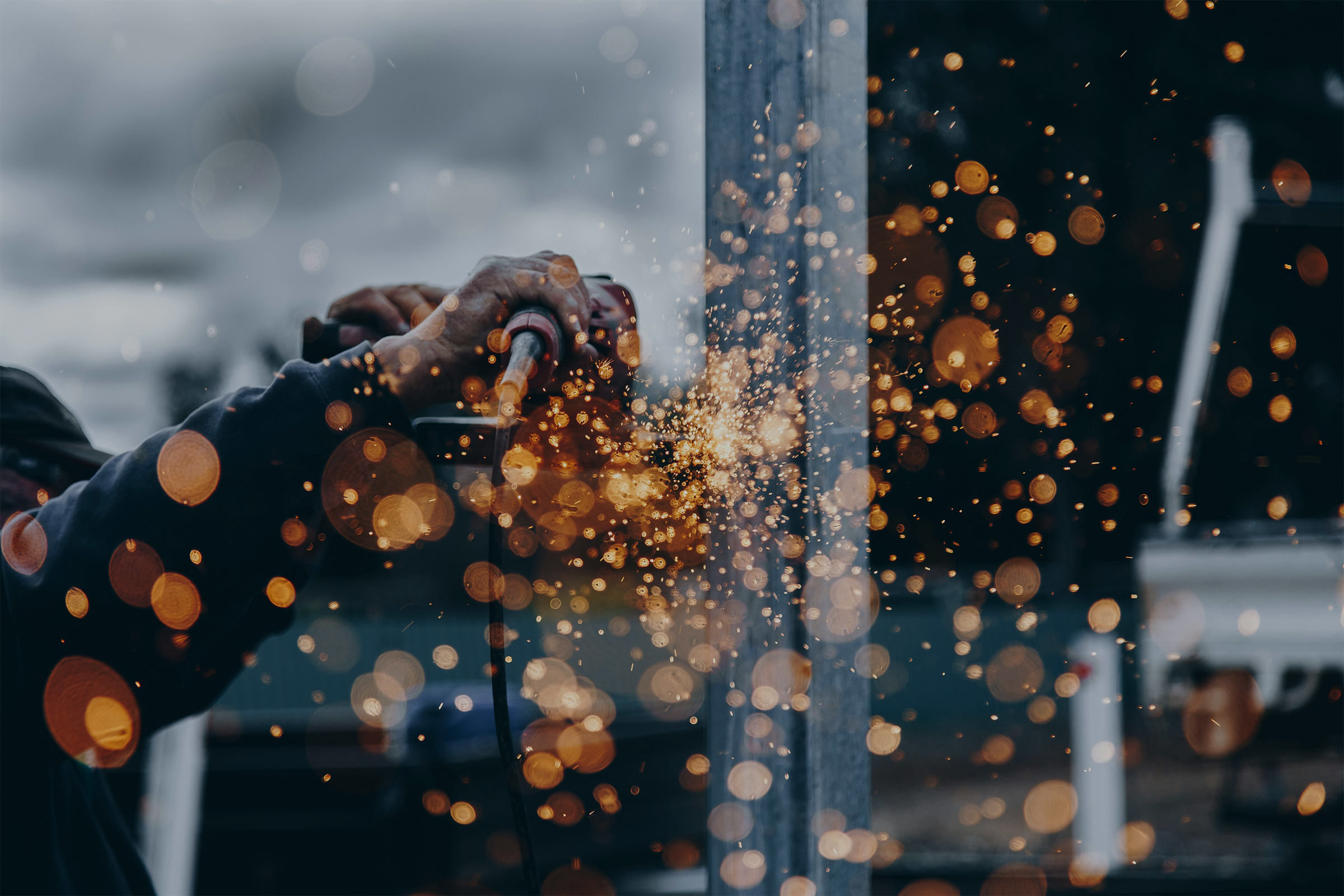
In product development, there are a number of steps that should be carried out in order to launch a new product. The overall objectives for any new product will almost certainly include earning a margin and generating a return on investment for the product development expenses as well as investment in production capability.
To achieve these goals for a manufactured product, it’s important that the start of production be smooth and as trouble-free as possible. In addition, it’s also critical that the products that are sold perform as promised. That means no defects during the first year of usage as well as no safety defects during the entire life of the product.
Getting these kinds of results is never an accident. To do this requires a level of structure and thoroughness in the development process. What are the key steps?
ISO 15288
The ISO/IEC 15288 is an international standard for systems engineering that describes an ideal set of steps to reach these goals. While this standard isn’t intended to be a comprehensive description of everything that must be done in product development, it does explain the general flow of information from initial planning of a product all the way to the end-of-life considerations that are increasingly important. There are four steps in this standard:
-
- The first step is to plan the product, including the reason for the product and, most importantly, the generation of a reasonable complete conceptual design.
- The second step is the overall development of the concept into a production-ready package, including a verified design and a validated system of manufacturing.
- The third step is ongoing or serial production of items that will be sold.
- The fourth step includes all of the things that are necessary to support products that are sold, including usage instructions, service and support, and recommendations for end-of-life disposal of the product.
For most manufacturing companies, the second step is the most critical. It’s also the step that has the most impact on the eventual financial results of any development project.
Understanding Verification and Validation
While the terms “verification” and “validation” are often used interchangeably, in quality systems they have very specific and limited meanings.
Verification is the development of information and other forms of evidence that show that the final product design will perform as intended, independent of manufacturing considerations.
Validation is a demonstration that a verified design can be translated into a physical product using the actual production processes that will be used to generate saleable products.
In short, verification is evidence that the design is sound, and validation is proof that the product can be made in the way the design intends.
The Chain of Validation
While verification is a separate subject that won’t be addressed in detail in this article, validation is the final confirmation that a new product will be delivered to customers in a form that is consistent with the latest plans and expectations.
Validating a production system for a new product progresses through two stages. To start, you must develop a plan for production. Then, you must put that plan into action in a controlled experiment to see if the plan actually works as desired.
Validation Planning
Here are the steps involved in planning for validation. They include the development of a production process as well as any initial trials of machines, tooling, and related items.
The foundation for a successful production outcome is to plan the process, analyze the process for potential flaws before investing in hardware, and then to use that analysis to develop a Control Plan that will be used to keep the process operating properly once saleable product is being made. The analysis tool that underpins this “chain” of events is Process Failure Modes and Effects Analysis, or PFMEA.
In PFMEA, each manufacturing process (fabrication and/or assembly) is analyzed for cause and effect relationships. Controls are then derived, with prevention controls acting against causes and detection controls acting against effects. These controls then form the basis for the Control Plan.
With Control Plan in hand, it’s then possible to put together first-rate work instructions for factory personnel, and to formulate a plan for making sure that all of the measurement tools (or gages) can be validated, which is called Measurement System Analysis, or MSA.
While doing this, flaws or weaknesses in the planned manufacturing process should be revealed, and then changes can be made before finalizing investment decisions.
It’s then possible to try out the entire plan, using the tooling and equipment, the intermediate end point of a serious plant-level review being the result. Any corrective action necessary can be carried out at that point.
Completion of Validation
Once plant management has been satisfied that all of the plans, equipment, instructions, and workforce preparedness are complete, it’s time to see if it all works properly under the approximate conditions of ongoing production. This is the final stage of validation.
This starts with a production trial run, which is sometimes called a final pilot run of production. Real products, suitable for sale, are made. To the greatest extent possible, this production run should be done at the planned maximum rate of production, using all of the tools, gages, and equipment that will be used after the product launch begins. It also means that properly trained people, the same people that will work on the product after launch, should be doing the manual elements of the processes.
Enough parts or products should be built so that reasonable statistical analysis can be done. Taken together with the run-at-rate condition previously stated, this usually required at least four and usually eight hours of production be completed.
These parts can then be used to validated the gaging system and to statistically assess the critical product characteristics (which were identified in the Design FMEA process).
If all of those outcomes are reasonable, then a sampling of the products generated during the Production Trial Run can be subjected to whatever physical tests for performance and durability might be necessary.
If those outcomes are successful, the entire “machine” for production can be formally approved both at the plant level and by any other important party (usually an industrial customer for a supplier or by the product planning and marketing staff for an end-point manufacturer).
PFMEA Is Critical
Process FMEA is vital in this entire set of events. A carefully considered PFMEA will be reduce the likelihood that anything will go wrong during the validation process. If something does go astray, the consequences are not trivial. The launch can be delayed, possibly missing key marketing dates, delaying or even reducing the revenue needed to pay for all of the investment in the project. Tooling and equipment purchases can go far over budget. Worst of all, defective product can be sold, and that can be damage your company’s reputation in a way that can take years to overcome.
Validation matters.